Ultrasonic phased array application ② - phased array ultrasonic testing scheme for mold steel
Background
Ultrasonic phased array technology originated from medical ultrasound testing. In the early 1970s, commercial phased array systems for medical diagnosis first appeared; In the early 21st century, portable, battery powered phased array instruments for industrial applications emerged.
The industrial phased array ultrasonic imaging technology adopts a new method of transmitting and receiving ultrasonic waves. By controlling the excitation time and order of each element in the transducer array, the phase relationship of the sound waves emitted (or received) by each element when they reach (or come from) a certain point in the object is changed, achieving changes in the focus and direction of the sound beam, and completing the acoustic imaging technology.
According to the Huygens principle, the wavefront of any ultrasonic wave can be seen as a combination of several sub wave sources emitting coherent ultrasonic waves. Conversely, coherent ultrasonic waves emitted by neatly arranged micro transducers (array probes) can form specific beams and wavefronts. By delaying the electrical pulses that excite each chip of the array probe according to a certain law (focusing law) through the controller, the shape and propagation direction of the ultrasonic beam can be changed with the variation of the delay law.
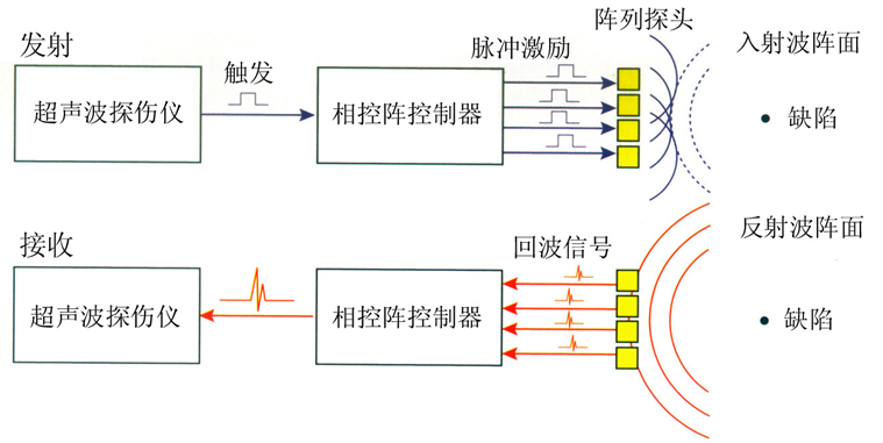
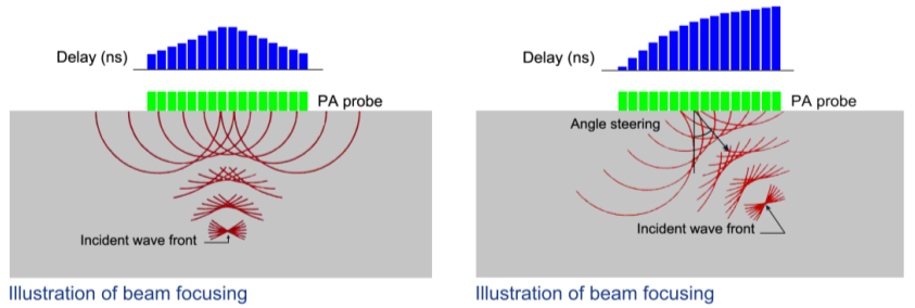
Testing methods and equipment
① Method: Industrial phased array ultrasound imaging technology, as a novel, efficient, and highly technological ultrasound testing method, is different from the A-ultrasound that we have been using routinely. Let's compare it with the table below:
Summary: From the comparison in the table above, it is not difficult to see the advantages of phased array technology compared to conventional ultrasonic testing technology:
1) The detection speed is fast. Due to the delayed excitation of the array probe in the probe through electronic methods, it performs linear scanning much faster than conventional manual and mechanical scanning;
2) Flexible to use, the phased array probe can freely control the focusing depth, deflection angle, beam width, and achieve longitudinal wave detection, transverse wave detection, and oblique injury detection;
3) In the inspection, there is no need for multi-dimensional scanning such as sawtooth, and only one-dimensional scanning is required to comprehensively inspect the weld seam, resulting in high detection efficiency;
4) In the detection process, there is no need to constantly change the angle based on the condition of the detection object. A probe can scan dozens or even hundreds of probe angles, greatly improving the detection ability;
5) Capable of achieving various imaging methods such as B/C/D/S, making defect detection more intuitive and clear;
6) Capable of achieving dynamic (several passive) focusing, greatly improving the ability to detect small defects, with a detection error of less than 0.1mm;
② Equipment: CTS-PA22A phased array ultrasonic testing instrument is a newly developed portable phased array testing instrument by Shantou Ultrasound; The instrument adopts a waterproof and oil resistant panel, with a fanless design and touchscreen operation, achieving full process recording of testing data. It is an advanced intelligent phased array ultrasonic testing equipment in China.
The application fields include the detection of conventional or special welds in steel structures, power plant boilers, pressure vessels, transmission pipelines, nuclear power, ships, oil tanks, storage tanks, ethylene pipelines, etc; Thorough inspection of aerospace aluminum alloy friction stir welded joints and composite material bonding structures; Inspection of blade roots, blades, bolts, etc. in the power industry; And for the detection of workpieces with limited moving space and other conventional ultrasonic testing occasions.
characteristic
1- Phased array detection function, dual channel conventional ultrasound detection function,
2- Equipped with a 3D process simulation model, it can customize exclusive testing processes for users and provide a complete set of solutions in a one-stop manner.
3-Equipped with image smoothing processing function, providing high-quality image display.
4- With dynamic deep focusing function, defects of different depths can achieve good detection resolution.
5-No fan cooling required, fully sealed waterproof and dustproof design with natural heat dissipation mode, suitable for various harsh testing environments.
The delay accuracy of 6-2.5ns can significantly suppress sidelobes, improve the longitudinal and transverse resolution of the sound beam, and improve imaging clarity by improving the accuracy of phase delay.
7-Conventional A-scan, phased array line scan, sector scan, and C-scan real-time fast imaging, continuous data recording using encoder, 100% raw data acquisition.
8- Supports the ACG and TCG curve compensation functions specified in ASME standards, solving problems such as uneven energy distribution and measurement errors during sector scanning.
The 9-focusing rule is automatically calculated and generated quickly based on the sound beam angle, focal length, scanning mode, probe and wedge parameters, and the sector scanning angle is automatically optimized step by step.
The 10-filter is available in three levels: 0.5-9.7MHz, 4.0-12.5MHz, and 6.7-20.8MHz. The pulse width is automatically optimized based on the probe frequency, highlighting excellent noise processing technology.
11-8.4 inch industrial grade, full WVGA resolution (800 × 600) TFT display screen, providing touch screen operation, providing excellent display effect outdoors or under strong light.
The user-friendly design of the 12 keyboard buttons is suitable for both left and right hands to operate simultaneously, and the one click shuttle can set various parameters simultaneously.
13-USB interface for fast data transfer and storage; The HDMI video interface enables the detection screen to expand infinitely.
14- The power supply is used for both AC and DC purposes, and two lithium batteries can be used for power supply at the same time. During power supply, the instrument can automatically switch the batteries according to the power level, ensuring that the instrument operates for more than 6 hours.
Performance indicators:
(See product color page for details)
Preparation before testing
a. Workpiece: According to the actual measurement on site, the size is approximately 2500mm × 100mm × 135mm, made of mold steel; Before testing, it is necessary to ensure that the appearance inspection is qualified and the surface roughness is not less than 25.4 μ M; As shown in Figures 1 and 2:
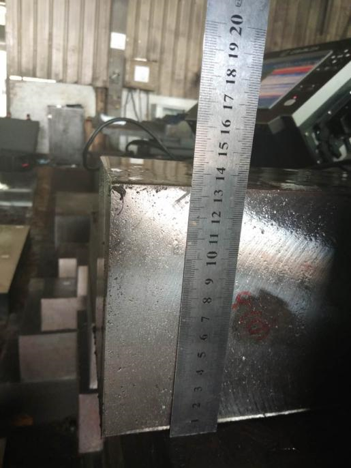
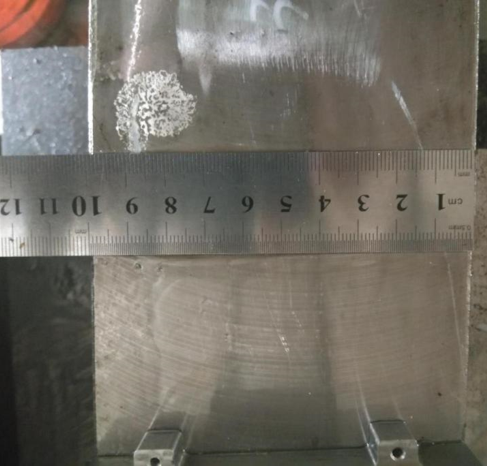
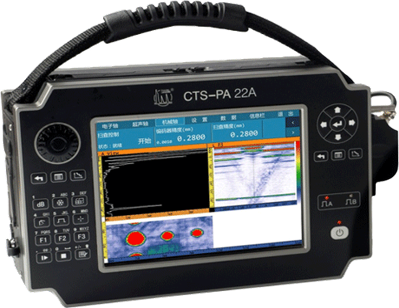
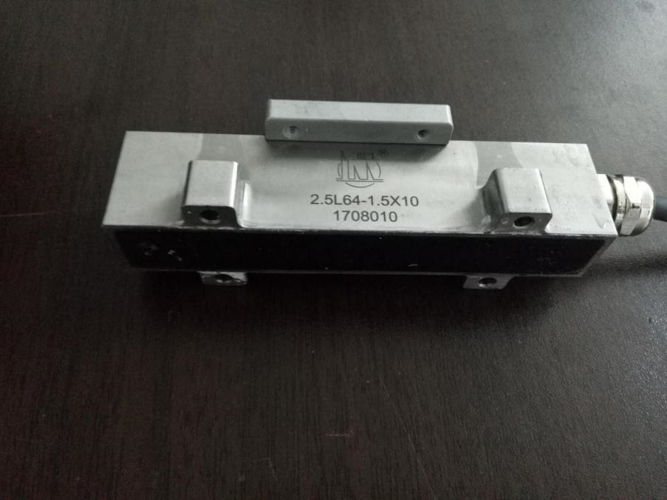
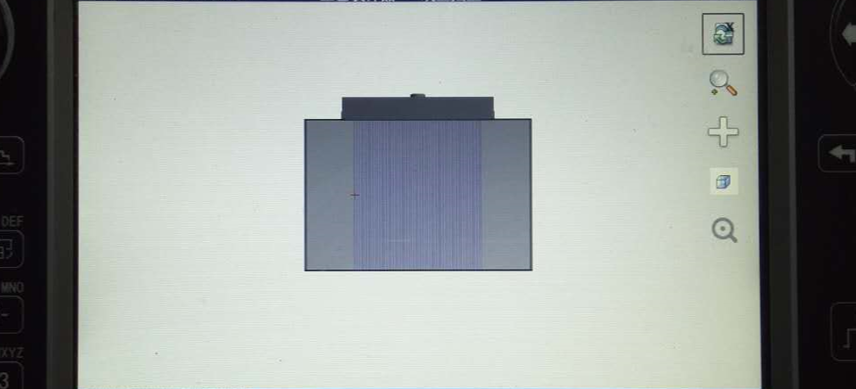
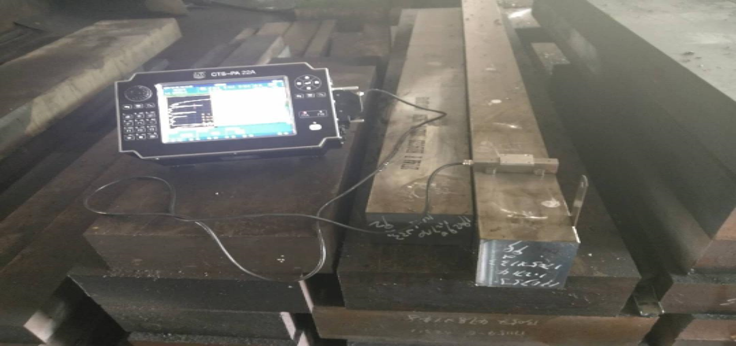
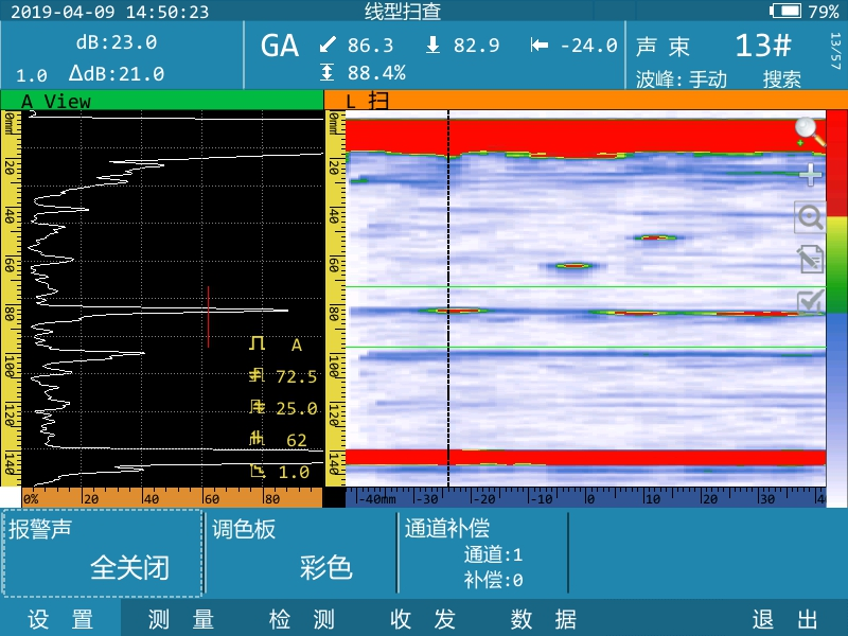
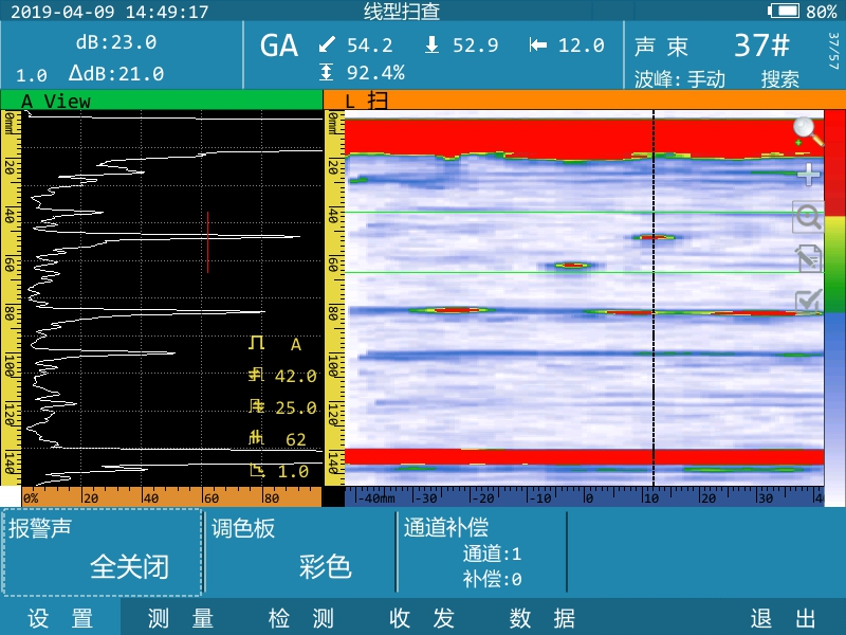
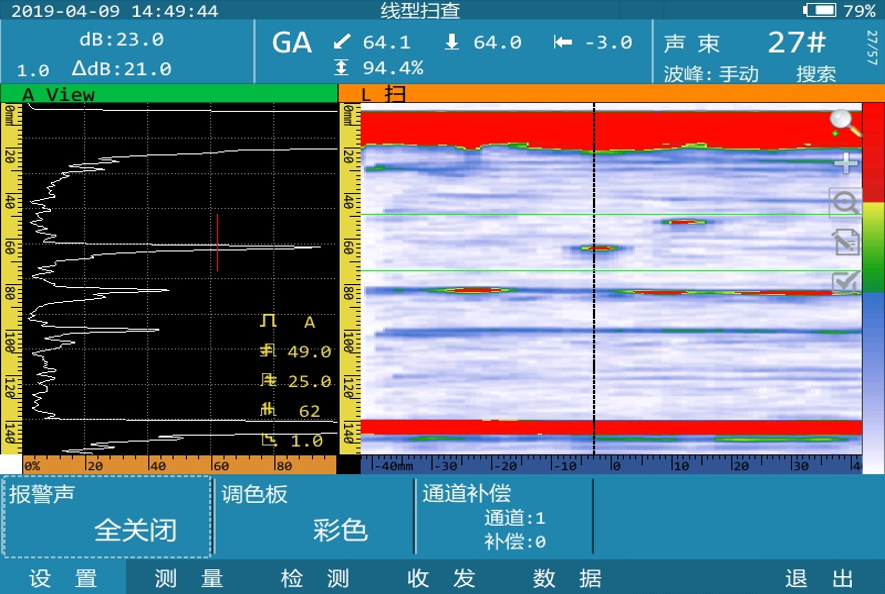