Location:Home > APPLICATION
The current application of non-destructive testing in new fields
Release time:2023-09-26
The non-destructive testing method that utilizes the principle of electromagnetic induction to non-destructive evaluate certain properties of conductive materials and their workpieces by detecting changes in induced eddy currents within the tested workpiece, or to detect defects, is called non-destructive testing. In industrial production, eddy current testing is one of the main means to control the quality of various metal materials and a few non-metals (such as graphite, carbon fiber composite materials, etc.) and their products. Compared with other non-destructive testing methods, eddy current testing is easier to achieve automation, especially for profiles such as pipes, rods, and wires, which have high testing results. The following introduces the applications of non-destructive testing in some new fields:
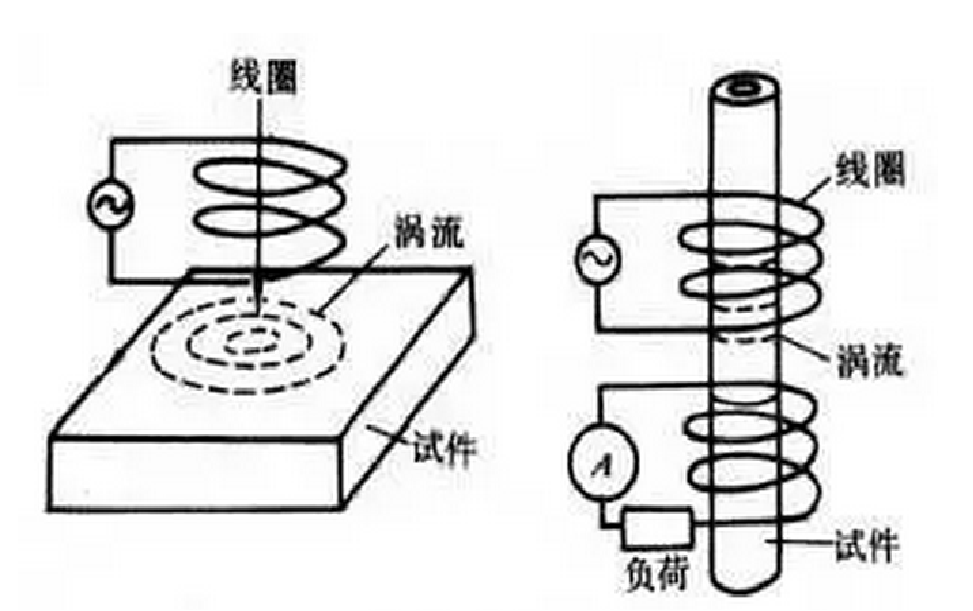
1.1 Thickness measurement
The application of thickness measurement mainly has two aspects: measurement of the thickness of the film layer on the metal substrate and measurement of the thickness of the metal sheet. The measurement of insulation layer thickness on non-magnetic metals is an important application field of eddy current thickness measurement. Due to the fact that non magnetic metals are all non-ferrous metals with high conductivity, measuring the thickness of their surface insulation layer essentially measures the distance between the probe coil and the base metal. In order to suppress the influence of changes in the conductivity of the substrate metal on the measurement results, a higher detection frequency is generally chosen. At this time, the influence of the substrate conductivity on the inductance component can be ignored, while the influence on the resistance component is still significant. Due to the fact that the inductance component is mainly affected by distance changes. The resistance component is mainly affected by changes in conductivity. Therefore, as long as the inductance of the probe impedance change signal is taken out from the circuit, and then zeroed and corrected, the change in insulation layer thickness can be measured.
When the surface of magnetic metal is covered with non-magnetic metal or insulation layer (such as chromium plating or paint layer on steel parts), electromagnetic induction method can also be used to measure its thickness. When the excitation current passes through the coil, a magnetic path is established between the detection coil and the magnetic substrate. Due to changes in the gap between the coil and the magnetic substrate (i.e. the influence of non magnetic film thickness), it will change the magnetic negativity of the magnetic circuit and cause changes in the magnetic flux in the magnetic circuit. Therefore, by measuring the induced voltage on the detection coil, a quantitative relationship curve between the induced voltage and the gap (i.e. film thickness) can be obtained, Then mark it on the dial of the indicating instrument, and the thickness of the film can be directly read from the indicating instrument in the future. When measuring the thickness of metal thin plates using eddy current method, the detection coil can use both reflection method and transmission method. The reflection method refers to the method where the transmitting and receiving coils of the probe are on the same side of the measured body, and the received signal is a signal of impedance amplitude change. The change in material thickness has a non-linear relationship with the impedance change of the receiving coil. Therefore, it is required to achieve nonlinear correction within the measuring instrument, which can result in significant measurement errors. The transmission method is based on the distribution of eddy current field generated by the probe line, that is, the phase lag of eddy current increases with depth at different depths. The thickness value of the tested material is directly obtained based on the phase difference between the received signal and the excitation signal, without the need for nonlinear correction.
1.2 Eddy Current Testing
Due to the skin effect of eddy current, eddy current testing can only be used to detect defects on the surface and near surface of metal workpieces. However, due to its advantages of simplicity, no need for coupling agents, and easy implementation of high-speed automatic detection, it has been widely used in the detection of metal materials and components. Eddy current testing can also be used for maintenance and inspection. Due to special working conditions (such as working at high temperature, high pressure, and high speed), certain mechanical products are often prone to fatigue and corrosion cracks during use. Although magnetic particle testing, penetration testing, and other methods are effective for these defects, eddy current testing is not only sensitive to these defects, but can also be used to inspect components coated with coatings such as paint and epoxy resin, as well as blind hole areas and threaded groove bottoms. It also causes cracks in structural components under the skin, which has attracted attention in the maintenance industry.
1.3 Material sorting
Eddy current testing is an important factor that affects the coil impedance, as the conductivity and magnetic permeability of the specimen are important factors. Therefore, the material of certain specimens can be evaluated by measuring the changes in conductivity or magnetic permeability of different specimens. The material testing of non-magnetic metal materials is generally carried out through the measurement of electrical conductivity. During testing, the test piece does not need to be further processed, as long as there is a small plane on the surface of the test piece (such as the requirement of 10-20mm for the 7501 eddy current conductivity meter) to place the probe. The detection is simple and feasible, and is suitable for rapid non-destructive inspection of certain properties of metal materials or parts. By measuring the conductivity, it is possible to identify the metal composition and impurity content, the heat treatment status and hardness of metals, and the sorting of mixtures of various metal materials or parts. It can be seen that the conductivity measured by eddy current method provides an effective method for material quality management and inspection. The material testing of ferromagnetic materials is generally carried out through the measurement of magnetic properties. For example, the strong magnetization method utilizes certain quantities in the hysteresis loop of magnetic materials as detection variables. Due to the fact that these quantities (such as saturation magnetic induction strength Bm, residual magnetism Br, coercive force Hc, etc.) are sensitive to the material of the specimen, there may be corresponding relationships between them and the microstructure, heat treatment state, and mechanical properties of the specimen. Therefore, as long as the values of certain variables in the hysteresis loop are detected, the heat treatment status and sorting mix of the material can be inferred based on this corresponding relationship. The weak magnetization method uses the initial magnetic permeability as the detection variable, and can directly use certain eddy current flaw detectors (such as FQR7505) for material sorting.
1.4 Metal surface rust detection
When rust occurs on the gold surface, the rust products (mainly metal oxides) have different physical properties from the base metal. The differences in their physical properties, especially between conductivity and magnetic permeability, can affect the reflection resistance and inductance of the eddy current probe coil, making it possible to use eddy current method to detect corrosion on metal surfaces. In order to detect corrosion on metal surfaces, we have developed a dual coil eddy current sensor, which uses experimentally determined detection rate excitation and corresponding detection circuits to detect corrosion on metal surfaces. According to our experiment, the lift off effect curve of the corroded specimen at a fixed frequency is approximately a straight line. The degree of corrosion on the metal surface can be accurately determined from the change in the slope of the straight line. For carbon steel parts, the more severe the surface corrosion, the smaller the slope of the straight line. After using a microcomputer data acquisition system, it is very convenient to complete the collection, conversion, and processing of detection signals. only
To move the detection probe up and down above the sample, the lift-off effect curve of the sample can be displayed on the screen. Then, the fitting line can be drawn through linear regression processing, and the fitting line can be drawn through linear regression processing to calculate the slope of the line. Then, compare this slope with the detection results of the standard sample, and those with smaller slope values will have more severe corrosion. As a new non-destructive testing method, eddy current testing technology and theoretical research have made rapid progress. With the development of electronic technology, especially computer and information processing technology, eddy current testing equipment is constantly moving towards microcomputerization and intelligence, and the quantitative evaluation and display technology for defects is constantly improving. It can be foreseen that the application of eddy current testing technology will become increasingly widespread.
1.5 Simulation detection of surface and near surface crack defects in metal
For subsurface cracks, as the depth of the defect increases, the time for the maximum induced magnetic field to appear will be longer; However, for surface cracks, the maximum value of the induced magnetic field for cracks of different depths occurs at almost the same time. This indicates that pulsed eddy current is more suitable for quantitative detection of deep subsurface cracks. In practical applications, the corresponding curve between the depth and the time when the maximum value of the induced magnetic field appears can be drawn based on the response data of artificial defects at different depths. After measuring the time when the maximum value of the defect response signal appears in actual testing, the depth of the defect can be determined by corresponding to the reference curve.
1.6 Quantitative detection and scanning imaging of corrosion defects
Quantitative detection of corrosion defect length, quantitative detection of corrosion defect depth using the zero crossing time of transient induced voltage signal, and quantitative detection of corrosion defect volume using the peak value of transient induced voltage signal. When using an eddy current array coil with 8 detection coils symmetrically arranged in the center of the bottom of the excitation coil to scan and process samples with simulated corrosion defects, there is a rule between the ratio of the maximum peak value of the eddy current response signal received by the two detection coils at the symmetrical position: for different corrosion depths, when the probe array is completely scanned by corrosion, the ratio is greater than or equal to 0.5; When the probe array is not completely scanned for corrosion, the ratio is less than or equal to 0.2. Therefore, this ratio can be used as a characteristic parameter to determine whether the detection coil has undergone corrosion, for probes that have not undergone corrosion. When displaying a corroded image, the scanning path it passes through will not be displayed. This can effectively eliminate image distortion.
1.7 Actual testing of in-service pipelines and pipelines
The China Special Equipment Testing and Research Center applied the InCotest pulse eddy current detector manufactured in the Netherlands to conduct actual testing on the in-service condensate oil pipeline of an oil and gas separation plant and the steam pipeline of a thermal power plant. Without removing the protective layer and insulation layer, two corrosion defects were found when using pulse eddy current technology to inspect the internal pipeline. The measurement results of these two corrosion depths using pulse eddy current method were compared with the ultrasonic measurement results under the conditions of removing the protective layer and insulation material. The maximum errors were 0.69 mm and 0.64 mm, respectively, which can meet the measurement accuracy requirements of engineering inspection standards.
New Applications of 1.8 Eddy Current Non destructive Testing Technology in the Steel Industry
Eddy current testing, as one of the five conventional non-destructive testing methods, is widely used in the steel industry, including metal rod and wire inspection, fatigue crack detection of structural components, identification of material composition and impurity content, identification of heat treatment status, mixed material sorting, measurement of thickness of metal thin plates, and many other aspects. In recent years, with the deepening of understanding of eddy current testing technology and the development of computers, instruments, and digital signal processing technology, eddy current non-destructive testing technology has made certain breakthroughs in the application of the steel industry. For some problems that were previously considered as detection limits or "impossible", solutions or ideas have been found. For example, some people have proposed online simulation testing of surface defects in high-temperature continuous casting slabs above 1100 ℃, which increases the temperature of traditional eddy current testing objects by several hundred degrees. A Swedish company has developed eddy current testing equipment for detecting 1000 ℃ high-temperature steel and other metal plates and billets. In addition, the application of eddy current detection has also extended to stainless steel capillary tubes, wire with a diameter less than 1mm, and liquid level detection in crystallizers.
1.8.1 Detection of Surface Defects in 1000 ℃ High Temperature Continuous Casting Slabs
The limitation of eddy current testing for high-temperature products mainly lies in the temperature that the probe can withstand. Traditional eddy current testing technology can detect temperatures up to 550 ℃ under high temperature conditions. If a water-cooled probe is used for testing, the temperature can still be increased. Jia Huiming and others developed high-temperature eddy current probes using special materials, using a combination of air cooling and water cooling to maintain the internal temperature of the sensor below 40 ℃ and withstand strong high-temperature radiation for a long time. The experiment shows that the high-temperature probe can be used to detect surface defects with a depth of 1.5mm, a width of 0.3mm, and a length of 10mm on the cast slab above 1100 ℃ online. This technology can effectively suppress the noise impact caused by vibration marks on the surface of the casting billet, and with the help of computer signal processing technology, achieve the positioning, quantitative analysis, and printing record of surface defects on the hot casting billet, providing a technical basis for online non-destructive testing of the continuous casting billet.
According to information, a Swedish company designed and manufactured a device based on eddy current technology that can inspect surface defects of steel and other metal plates and billets at around 1000 ℃. This device can ensure that both almost vertical directions of the steel surface are scanned. By using an analyzer composed of computers, the input signals can be divided into three main categories: serious defects, harmless defects, and unrecognized defects, and the location of any defects can be identified. This device can accurately determine the position of 0.5mm deep scratches on the surface of the blank.
1.8.2 Detection of stainless steel capillary tubes
Although electromagnetic eddy current testing is feasible for offline or online non-destructive testing of extremely small pipe diameters such as stainless steel capillaries, special probes must be configured to achieve satisfactory results. Due to the extremely small diameter of the capillary tube, the current technology level is not yet able to produce an internal penetration probe, nor can point probes be used for detection. Only external penetration probes can be used for detection. The differential external penetration probe jointly developed by Xi'an Jiaotong University and Ederson (Xiamen) Electronics Co., Ltd. is equipped with a specially designed advanced external penetration special probe after calculating and optimizing the width and thickness of the coil, the span between the two coils, the gap between the probe and the capillary, and the wire diameter. At a detection frequency of 666kHz Φ 1mm and Φ A 0.45mm stainless steel capillary tube was used for detection, and good results were achieved.
1.8.3 Online detection of steel wire
There are generally two methods used for online detection of steel wires: one is the rotary detection type, where the eddy current detector rotates at high speed around the steel wire. This method is mainly used to detect cracks, scratches, and wire drawing scratches that extend longitudinally along the steel wire. The trajectory of the detector is spiral shaped relative to the movement of the steel wire. Using multiple detectors in parallel for high-speed rotation can achieve 100% inspection, but its sensitivity for surface inspection is limited. It is difficult to maintain a constant distance between the detector and the steel wire. As the gap increases, the sensitivity decreases. If the steel wire is eccentric, the gap will change. The use of high-speed processors can automatically sense gaps and continuously compensate, improving the sensitivity of the system. The other type is the surround coil type. The steel wire passes through the circular coil, and the transducer effectively checks the distribution of eddy currents in one section and compares it with the previous section. It is suitable for detecting point defects and circumferential cracks, and has high sensitivity for transverse cracks, V-shaped cracks, inclusions, pits, and folds. Fast detection speed and wide detection diameter range.
The driving current of the surround coil type is higher than that of the rotary detection type, which has better depth penetration. The system has good stability and is not affected by temperature changes and other factors. When the magnetic material is below the Curie point of 800 ℃, magnetic saturation will suppress the signal, but it can be avoided by adjusting the magnetic field strength to improve sensitivity. At present, most of the methods use surround coil, and a combination of the above two methods can also be used. Eddy current technology has been well applied in wire drawing, oil tempering production lines, cold heading steel wire or spring steel wire production. The water-cooled coil is used to detect wire rods with a temperature exceeding 1100 ℃, and its detection speed exceeds 500km/h.
1.8.4 Liquid level detection
The precise detection of mold liquid level is the key to achieving automatic liquid level control in the continuous casting production process. The eddy current type liquid steel level gauge has significant advantages such as fast reaction speed, high measurement accuracy, no need for special safety protection, and easy installation and maintenance. Its practicality has made rapid progress. Song Dongfei introduced the use of domestically produced RAM series vortex type liquid steel level controllers in the renovation of Pangang. The measurement system uses an eddy current sensor to measure the liquid level of molten steel. The 50 kHz high-frequency signal generated by the oscillator is supplied to the primary coil (excitation coil) of the sensor. Due to the influence of eddy current in the molten steel, the alternating magnetic field generated by the primary coil changes with the height of the liquid level. A voltage V will be generated within the secondary coil (measuring coil) that varies in direct proportion to the intensity of the magnetic field passing through the coil γ V2, thus the differential voltage (V1-V2) varies with the liquid level height. adopt
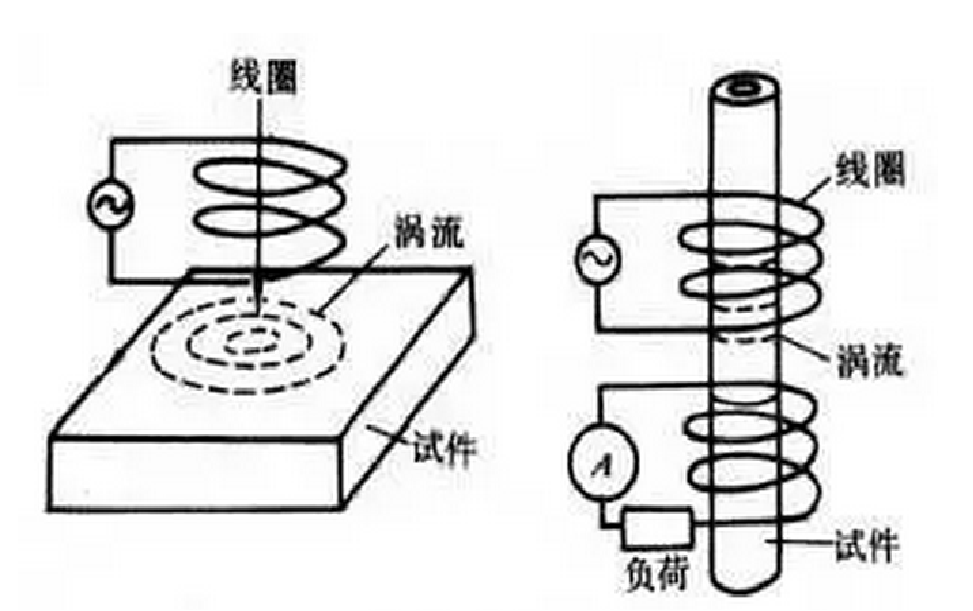
1.1 Thickness measurement
The application of thickness measurement mainly has two aspects: measurement of the thickness of the film layer on the metal substrate and measurement of the thickness of the metal sheet. The measurement of insulation layer thickness on non-magnetic metals is an important application field of eddy current thickness measurement. Due to the fact that non magnetic metals are all non-ferrous metals with high conductivity, measuring the thickness of their surface insulation layer essentially measures the distance between the probe coil and the base metal. In order to suppress the influence of changes in the conductivity of the substrate metal on the measurement results, a higher detection frequency is generally chosen. At this time, the influence of the substrate conductivity on the inductance component can be ignored, while the influence on the resistance component is still significant. Due to the fact that the inductance component is mainly affected by distance changes. The resistance component is mainly affected by changes in conductivity. Therefore, as long as the inductance of the probe impedance change signal is taken out from the circuit, and then zeroed and corrected, the change in insulation layer thickness can be measured.
When the surface of magnetic metal is covered with non-magnetic metal or insulation layer (such as chromium plating or paint layer on steel parts), electromagnetic induction method can also be used to measure its thickness. When the excitation current passes through the coil, a magnetic path is established between the detection coil and the magnetic substrate. Due to changes in the gap between the coil and the magnetic substrate (i.e. the influence of non magnetic film thickness), it will change the magnetic negativity of the magnetic circuit and cause changes in the magnetic flux in the magnetic circuit. Therefore, by measuring the induced voltage on the detection coil, a quantitative relationship curve between the induced voltage and the gap (i.e. film thickness) can be obtained, Then mark it on the dial of the indicating instrument, and the thickness of the film can be directly read from the indicating instrument in the future. When measuring the thickness of metal thin plates using eddy current method, the detection coil can use both reflection method and transmission method. The reflection method refers to the method where the transmitting and receiving coils of the probe are on the same side of the measured body, and the received signal is a signal of impedance amplitude change. The change in material thickness has a non-linear relationship with the impedance change of the receiving coil. Therefore, it is required to achieve nonlinear correction within the measuring instrument, which can result in significant measurement errors. The transmission method is based on the distribution of eddy current field generated by the probe line, that is, the phase lag of eddy current increases with depth at different depths. The thickness value of the tested material is directly obtained based on the phase difference between the received signal and the excitation signal, without the need for nonlinear correction.
1.2 Eddy Current Testing
Due to the skin effect of eddy current, eddy current testing can only be used to detect defects on the surface and near surface of metal workpieces. However, due to its advantages of simplicity, no need for coupling agents, and easy implementation of high-speed automatic detection, it has been widely used in the detection of metal materials and components. Eddy current testing can also be used for maintenance and inspection. Due to special working conditions (such as working at high temperature, high pressure, and high speed), certain mechanical products are often prone to fatigue and corrosion cracks during use. Although magnetic particle testing, penetration testing, and other methods are effective for these defects, eddy current testing is not only sensitive to these defects, but can also be used to inspect components coated with coatings such as paint and epoxy resin, as well as blind hole areas and threaded groove bottoms. It also causes cracks in structural components under the skin, which has attracted attention in the maintenance industry.
1.3 Material sorting
Eddy current testing is an important factor that affects the coil impedance, as the conductivity and magnetic permeability of the specimen are important factors. Therefore, the material of certain specimens can be evaluated by measuring the changes in conductivity or magnetic permeability of different specimens. The material testing of non-magnetic metal materials is generally carried out through the measurement of electrical conductivity. During testing, the test piece does not need to be further processed, as long as there is a small plane on the surface of the test piece (such as the requirement of 10-20mm for the 7501 eddy current conductivity meter) to place the probe. The detection is simple and feasible, and is suitable for rapid non-destructive inspection of certain properties of metal materials or parts. By measuring the conductivity, it is possible to identify the metal composition and impurity content, the heat treatment status and hardness of metals, and the sorting of mixtures of various metal materials or parts. It can be seen that the conductivity measured by eddy current method provides an effective method for material quality management and inspection. The material testing of ferromagnetic materials is generally carried out through the measurement of magnetic properties. For example, the strong magnetization method utilizes certain quantities in the hysteresis loop of magnetic materials as detection variables. Due to the fact that these quantities (such as saturation magnetic induction strength Bm, residual magnetism Br, coercive force Hc, etc.) are sensitive to the material of the specimen, there may be corresponding relationships between them and the microstructure, heat treatment state, and mechanical properties of the specimen. Therefore, as long as the values of certain variables in the hysteresis loop are detected, the heat treatment status and sorting mix of the material can be inferred based on this corresponding relationship. The weak magnetization method uses the initial magnetic permeability as the detection variable, and can directly use certain eddy current flaw detectors (such as FQR7505) for material sorting.
1.4 Metal surface rust detection
When rust occurs on the gold surface, the rust products (mainly metal oxides) have different physical properties from the base metal. The differences in their physical properties, especially between conductivity and magnetic permeability, can affect the reflection resistance and inductance of the eddy current probe coil, making it possible to use eddy current method to detect corrosion on metal surfaces. In order to detect corrosion on metal surfaces, we have developed a dual coil eddy current sensor, which uses experimentally determined detection rate excitation and corresponding detection circuits to detect corrosion on metal surfaces. According to our experiment, the lift off effect curve of the corroded specimen at a fixed frequency is approximately a straight line. The degree of corrosion on the metal surface can be accurately determined from the change in the slope of the straight line. For carbon steel parts, the more severe the surface corrosion, the smaller the slope of the straight line. After using a microcomputer data acquisition system, it is very convenient to complete the collection, conversion, and processing of detection signals. only
To move the detection probe up and down above the sample, the lift-off effect curve of the sample can be displayed on the screen. Then, the fitting line can be drawn through linear regression processing, and the fitting line can be drawn through linear regression processing to calculate the slope of the line. Then, compare this slope with the detection results of the standard sample, and those with smaller slope values will have more severe corrosion. As a new non-destructive testing method, eddy current testing technology and theoretical research have made rapid progress. With the development of electronic technology, especially computer and information processing technology, eddy current testing equipment is constantly moving towards microcomputerization and intelligence, and the quantitative evaluation and display technology for defects is constantly improving. It can be foreseen that the application of eddy current testing technology will become increasingly widespread.
1.5 Simulation detection of surface and near surface crack defects in metal
For subsurface cracks, as the depth of the defect increases, the time for the maximum induced magnetic field to appear will be longer; However, for surface cracks, the maximum value of the induced magnetic field for cracks of different depths occurs at almost the same time. This indicates that pulsed eddy current is more suitable for quantitative detection of deep subsurface cracks. In practical applications, the corresponding curve between the depth and the time when the maximum value of the induced magnetic field appears can be drawn based on the response data of artificial defects at different depths. After measuring the time when the maximum value of the defect response signal appears in actual testing, the depth of the defect can be determined by corresponding to the reference curve.
1.6 Quantitative detection and scanning imaging of corrosion defects
Quantitative detection of corrosion defect length, quantitative detection of corrosion defect depth using the zero crossing time of transient induced voltage signal, and quantitative detection of corrosion defect volume using the peak value of transient induced voltage signal. When using an eddy current array coil with 8 detection coils symmetrically arranged in the center of the bottom of the excitation coil to scan and process samples with simulated corrosion defects, there is a rule between the ratio of the maximum peak value of the eddy current response signal received by the two detection coils at the symmetrical position: for different corrosion depths, when the probe array is completely scanned by corrosion, the ratio is greater than or equal to 0.5; When the probe array is not completely scanned for corrosion, the ratio is less than or equal to 0.2. Therefore, this ratio can be used as a characteristic parameter to determine whether the detection coil has undergone corrosion, for probes that have not undergone corrosion. When displaying a corroded image, the scanning path it passes through will not be displayed. This can effectively eliminate image distortion.
1.7 Actual testing of in-service pipelines and pipelines
The China Special Equipment Testing and Research Center applied the InCotest pulse eddy current detector manufactured in the Netherlands to conduct actual testing on the in-service condensate oil pipeline of an oil and gas separation plant and the steam pipeline of a thermal power plant. Without removing the protective layer and insulation layer, two corrosion defects were found when using pulse eddy current technology to inspect the internal pipeline. The measurement results of these two corrosion depths using pulse eddy current method were compared with the ultrasonic measurement results under the conditions of removing the protective layer and insulation material. The maximum errors were 0.69 mm and 0.64 mm, respectively, which can meet the measurement accuracy requirements of engineering inspection standards.
New Applications of 1.8 Eddy Current Non destructive Testing Technology in the Steel Industry
Eddy current testing, as one of the five conventional non-destructive testing methods, is widely used in the steel industry, including metal rod and wire inspection, fatigue crack detection of structural components, identification of material composition and impurity content, identification of heat treatment status, mixed material sorting, measurement of thickness of metal thin plates, and many other aspects. In recent years, with the deepening of understanding of eddy current testing technology and the development of computers, instruments, and digital signal processing technology, eddy current non-destructive testing technology has made certain breakthroughs in the application of the steel industry. For some problems that were previously considered as detection limits or "impossible", solutions or ideas have been found. For example, some people have proposed online simulation testing of surface defects in high-temperature continuous casting slabs above 1100 ℃, which increases the temperature of traditional eddy current testing objects by several hundred degrees. A Swedish company has developed eddy current testing equipment for detecting 1000 ℃ high-temperature steel and other metal plates and billets. In addition, the application of eddy current detection has also extended to stainless steel capillary tubes, wire with a diameter less than 1mm, and liquid level detection in crystallizers.
1.8.1 Detection of Surface Defects in 1000 ℃ High Temperature Continuous Casting Slabs
The limitation of eddy current testing for high-temperature products mainly lies in the temperature that the probe can withstand. Traditional eddy current testing technology can detect temperatures up to 550 ℃ under high temperature conditions. If a water-cooled probe is used for testing, the temperature can still be increased. Jia Huiming and others developed high-temperature eddy current probes using special materials, using a combination of air cooling and water cooling to maintain the internal temperature of the sensor below 40 ℃ and withstand strong high-temperature radiation for a long time. The experiment shows that the high-temperature probe can be used to detect surface defects with a depth of 1.5mm, a width of 0.3mm, and a length of 10mm on the cast slab above 1100 ℃ online. This technology can effectively suppress the noise impact caused by vibration marks on the surface of the casting billet, and with the help of computer signal processing technology, achieve the positioning, quantitative analysis, and printing record of surface defects on the hot casting billet, providing a technical basis for online non-destructive testing of the continuous casting billet.
According to information, a Swedish company designed and manufactured a device based on eddy current technology that can inspect surface defects of steel and other metal plates and billets at around 1000 ℃. This device can ensure that both almost vertical directions of the steel surface are scanned. By using an analyzer composed of computers, the input signals can be divided into three main categories: serious defects, harmless defects, and unrecognized defects, and the location of any defects can be identified. This device can accurately determine the position of 0.5mm deep scratches on the surface of the blank.
1.8.2 Detection of stainless steel capillary tubes
Although electromagnetic eddy current testing is feasible for offline or online non-destructive testing of extremely small pipe diameters such as stainless steel capillaries, special probes must be configured to achieve satisfactory results. Due to the extremely small diameter of the capillary tube, the current technology level is not yet able to produce an internal penetration probe, nor can point probes be used for detection. Only external penetration probes can be used for detection. The differential external penetration probe jointly developed by Xi'an Jiaotong University and Ederson (Xiamen) Electronics Co., Ltd. is equipped with a specially designed advanced external penetration special probe after calculating and optimizing the width and thickness of the coil, the span between the two coils, the gap between the probe and the capillary, and the wire diameter. At a detection frequency of 666kHz Φ 1mm and Φ A 0.45mm stainless steel capillary tube was used for detection, and good results were achieved.
1.8.3 Online detection of steel wire
There are generally two methods used for online detection of steel wires: one is the rotary detection type, where the eddy current detector rotates at high speed around the steel wire. This method is mainly used to detect cracks, scratches, and wire drawing scratches that extend longitudinally along the steel wire. The trajectory of the detector is spiral shaped relative to the movement of the steel wire. Using multiple detectors in parallel for high-speed rotation can achieve 100% inspection, but its sensitivity for surface inspection is limited. It is difficult to maintain a constant distance between the detector and the steel wire. As the gap increases, the sensitivity decreases. If the steel wire is eccentric, the gap will change. The use of high-speed processors can automatically sense gaps and continuously compensate, improving the sensitivity of the system. The other type is the surround coil type. The steel wire passes through the circular coil, and the transducer effectively checks the distribution of eddy currents in one section and compares it with the previous section. It is suitable for detecting point defects and circumferential cracks, and has high sensitivity for transverse cracks, V-shaped cracks, inclusions, pits, and folds. Fast detection speed and wide detection diameter range.
The driving current of the surround coil type is higher than that of the rotary detection type, which has better depth penetration. The system has good stability and is not affected by temperature changes and other factors. When the magnetic material is below the Curie point of 800 ℃, magnetic saturation will suppress the signal, but it can be avoided by adjusting the magnetic field strength to improve sensitivity. At present, most of the methods use surround coil, and a combination of the above two methods can also be used. Eddy current technology has been well applied in wire drawing, oil tempering production lines, cold heading steel wire or spring steel wire production. The water-cooled coil is used to detect wire rods with a temperature exceeding 1100 ℃, and its detection speed exceeds 500km/h.
1.8.4 Liquid level detection
The precise detection of mold liquid level is the key to achieving automatic liquid level control in the continuous casting production process. The eddy current type liquid steel level gauge has significant advantages such as fast reaction speed, high measurement accuracy, no need for special safety protection, and easy installation and maintenance. Its practicality has made rapid progress. Song Dongfei introduced the use of domestically produced RAM series vortex type liquid steel level controllers in the renovation of Pangang. The measurement system uses an eddy current sensor to measure the liquid level of molten steel. The 50 kHz high-frequency signal generated by the oscillator is supplied to the primary coil (excitation coil) of the sensor. Due to the influence of eddy current in the molten steel, the alternating magnetic field generated by the primary coil changes with the height of the liquid level. A voltage V will be generated within the secondary coil (measuring coil) that varies in direct proportion to the intensity of the magnetic field passing through the coil γ V2, thus the differential voltage (V1-V2) varies with the liquid level height. adopt